1. Fuel Nozzle In Jet Engine
General Electric (GE) has been quick to use to render parts of their jet engine GE9X in 2015. This engine generates upto 100,000 pounds of thrust and design for Boeing 777X. Each GE9X was equipped with 19 sets of new 3D printed fuel nozzle which is immpossible to make using conventional methods. Conventional fuel nozzles that had more than a dozen welded parts. This new 3D printed nozzle helped reduce weight by 25% and increase fuel efficiency comparing with conventional design. Up to Aug 2021, GE has shipped 100,000th 3D printed fuel nozzle.

2. Roof Bracket for BMW i8 Roadster
BMW has been using 3D printing for more than 25 years to speed up the development work of for each new model. Recently, BMW is leading the way in the use of 3D printing for mass production in the automotive industry by creating the first metal 3D printed part to be successfully produced for i8 Roadster.
The part is a roof bracket. With the help of 3D printing, this bracket now can be made of aluminium alloy in complex geometry design. This make it much lighter than conventional injection-moulded plastic bracket but is still considerably stiffer. The bracket makes the soft top of the automobile quickly raise and lower and fold and unfold in a zigzag configuration. It wasn’t an easy part to design. It needed to lift, push and pull the weight of the roof, and its design was necessarily complex, making it impossible to cast.
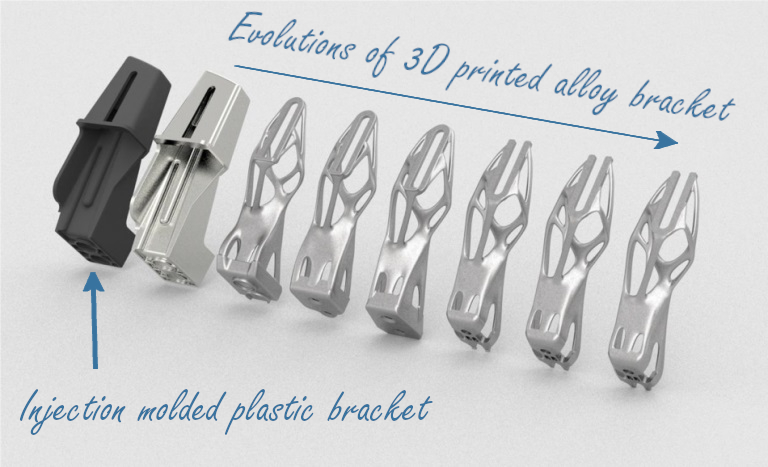
3. Customized Prostheses
3D printing is used in prostheses has become a new trend. In addition to being able to develop next-generation products, additive manufacturing is also used for aesthetically pleasing and practical features. Prostheses for above and below the knee amputees offer patients revolutionary personalization in terms of color and design. UNYQ ,a leader in the field of 3D-printed prosthetic wears, is working on manufacturing an entire leg by 3D printing . UNYQ provides its patients with an app to create the 3D-printed prostheses: Color, design and surface can be selected, then measurements are taken in a clinic to finally print the prosthesis using 3D-printing.
